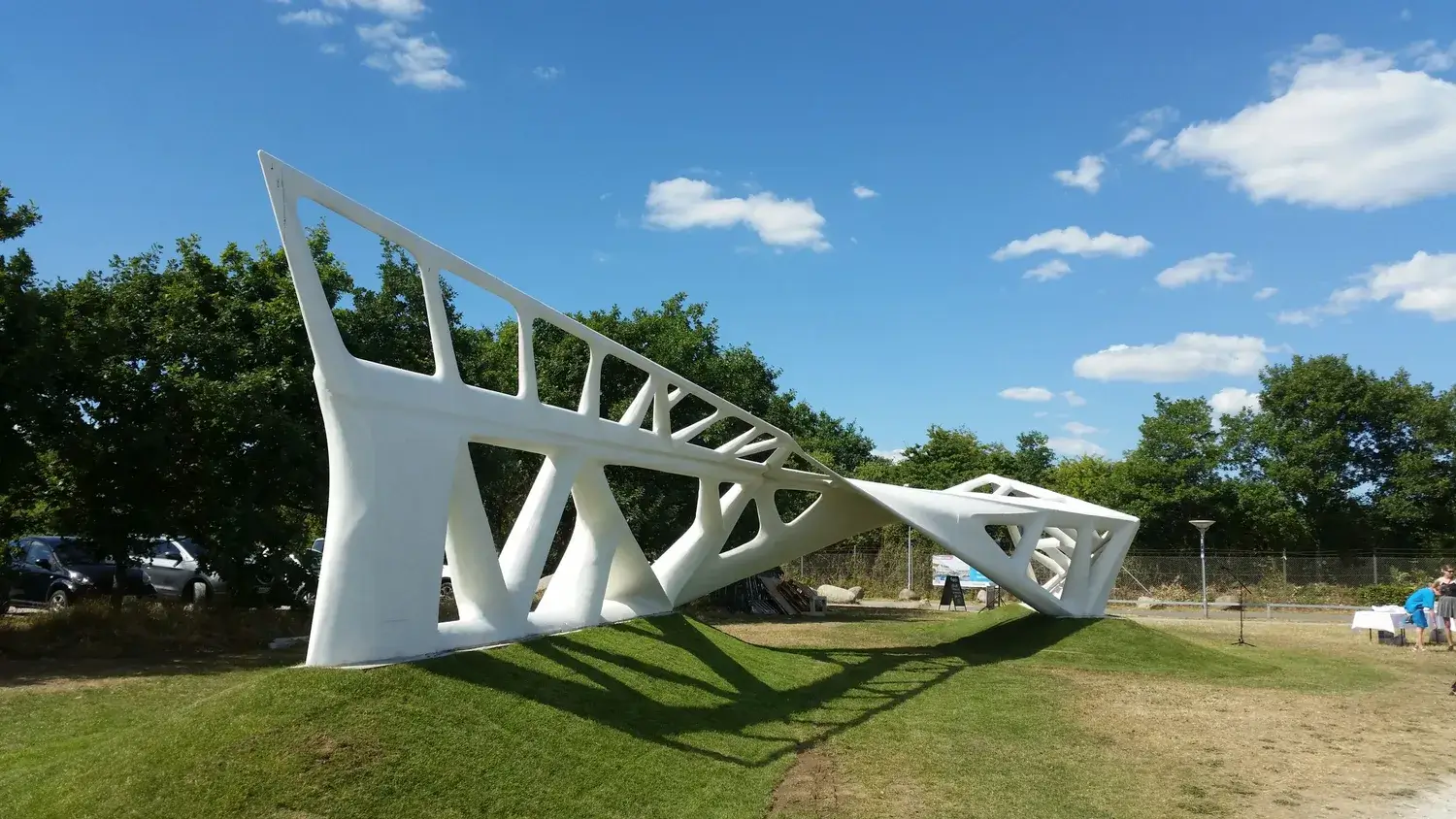
TUTUSTU JULKAISUIHIMME
Tervetuloa Hi-Conin tietopankkiin, joka on paras tietolähde innovatiivisista ratkaisuistamme ja ultrakorkealujuusbetonisista (UHPC) tuotteistamme. Johtavana UHPC-valmistajana jo vuodesta 2001 lähtien olemme erikoistuneet valmistamaan tyylikkäitä ja räätälöityjä parvekkeita, portaita ja julkisivuja käyttämällä omaa betonityyppiämme, CRC i2®.
Tietopankkimme on tarkoitettu tarjoamaan arvokkaita näkemyksiä, testituloksia, dokumentaatiota, laskelmia ja tuoteselostuksia asiakkaillemme, kumppaneillemme ja muille betonista kiinnostuneille. Olitpa nykyinen tai tuleva asiakkaamme, tutkija tai vain utelias tietämään lisää betonistamme, kutsumme sinut tutustumaan materiaaliimme CRC i2®, ja sen loputtomiin mahdollisuuksiin.
Toivomme, että nautit sukeltamisesta universumiimme ja tutustumisesta materiaaliimme paremmin. Jos sinulla on kysymyksiä tai ehdotuksia aiheista, joita haluaisit meidän käsittelevän, älä epäröi ottaa meihin yhteyttä käyttämällä sivun alareunassa olevaa lomaketta. Olemme aina innokkaita saamaan palautetta, ja auttamaan sinua oppimaan lisää vallankumouksellisista betoniratkaisuistamme.
Tiedätkö mitä CRC i2 -ultrakorkealujuusbetoni on? Lue siitä alla olevasta linkistä.