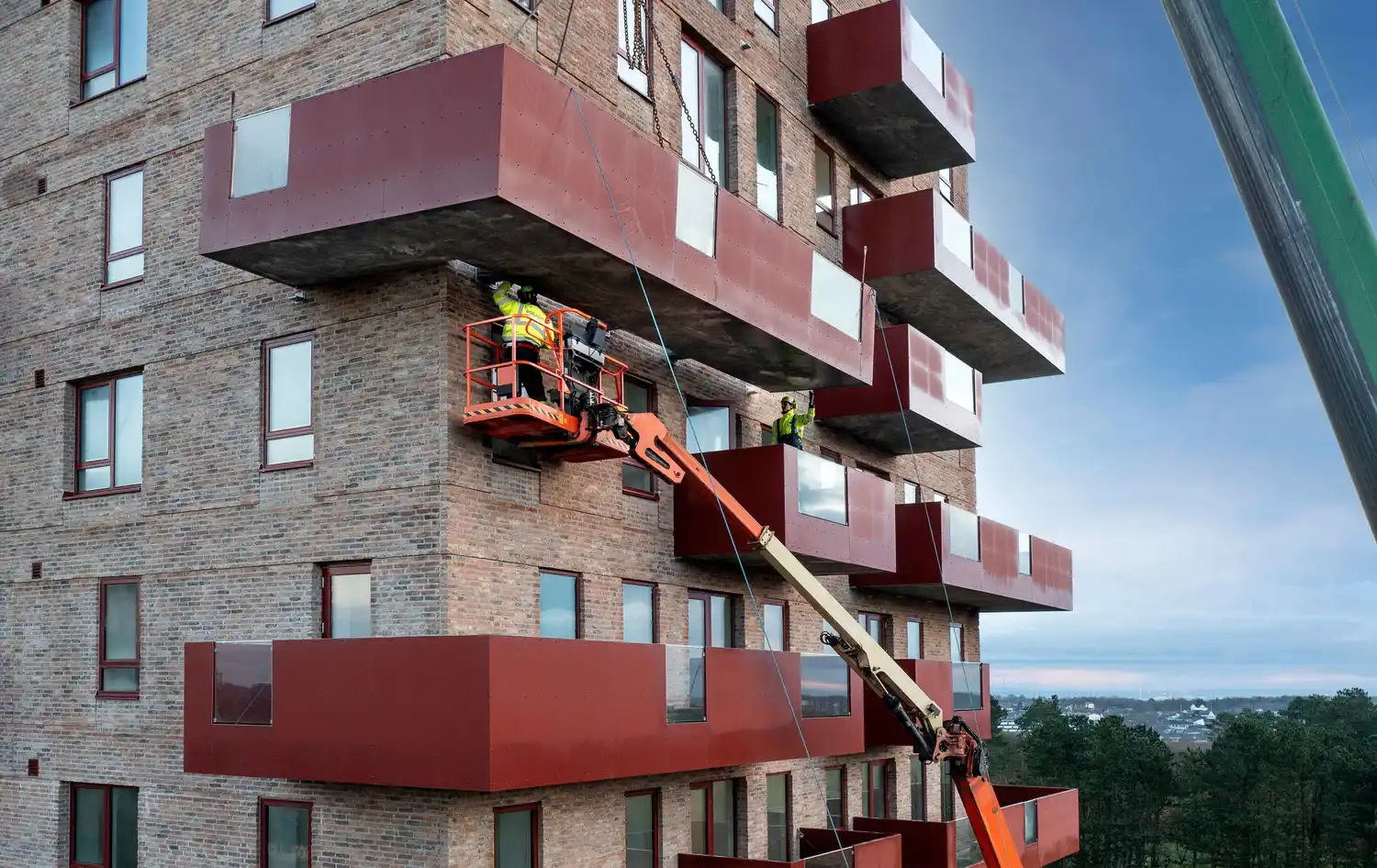
29. May 2025
In the test shown above, we see satisfactory behavior of beams with short steel fibers, while the other fiber type would not be suitable for CRC. Although ductility is an important and integral part of the behavior in CRC, we do not use it directly in our calculations. However, crack control is important for durability, stiffness, deflections, and aesthetic reasons. Ductility is also part of the reason for the effect we see in our "cold bending" tests.
Since we need to sell our products every day, we cannot just be satisfied with finding the fiber type and content that gives us the highest strength and toughness. If that were the case, Bache already achieved excellent results back in 1986/87. We need to find the best compromise between performance and price in each case (with a certain minimum performance) to be competitive— and performance in this case also relates to workability. Some fibers that provide good mechanical properties result in very poor workability (something I will address in a later post). Over the years, we have tested many different types of fibers and will continue to do so to take advantage of developments in the field. This knowledge is important for designing the right material for each task.
Based on this knowledge—and the work we have done over the years in this field—we want to be able to decide for each project which fiber type and content are best suited. This sometimes brings us into conflict with the requirements of a specific project, where the provider (or their advisor) specifies a certain fiber content without considering the fiber's dimensions and length/diameter ratio.
We are always open to discussion—but unfortunately, this is not always the case for the provider. Let us know if you have had similar considerations—or if you prefer relatively simple rules that are easy to relate to and perhaps provide better security. We also welcome your comments or questions. This post has been a (relatively) brief review of some of the parameters we consider when ensuring the necessary toughness for a construction, but we hope it has still been of interest.
We are ready to assist you with your project!
FILL OUT THE FORM AND WE WILL CONTACT YOU