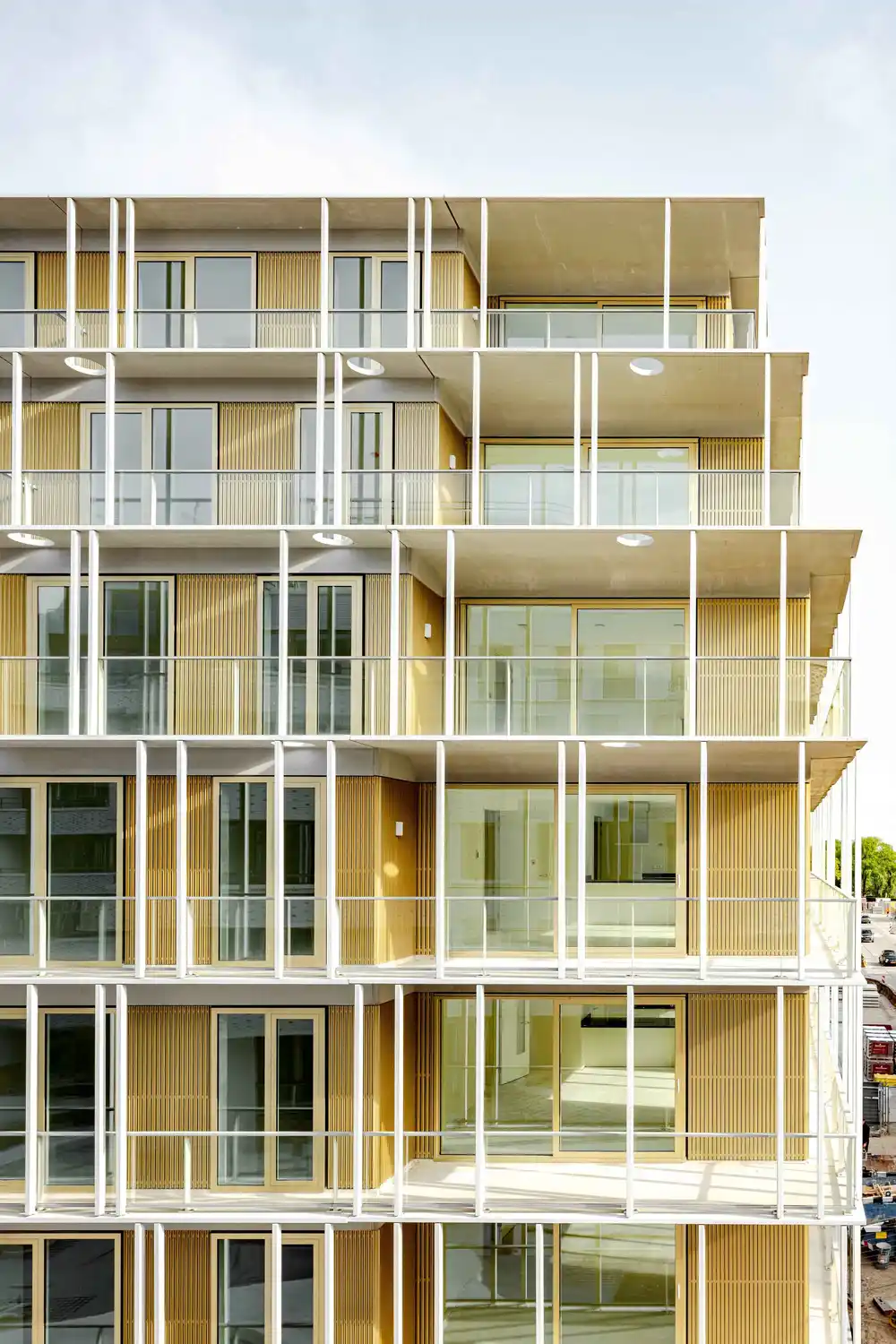
11. July 2025
When working with Ultra High Performance Concrete (UHPC) for many years, you encounter many claims of being a world leader in the material. This is also a claim we have made ourselves, but since Hi-Con only produces elements in UHPC and has never worked with traditional concrete, we believe our claim is justified, as we have produced more than 70,000 tons of structural elements in CRC over the years.
You have probably already noticed that we use many abbreviations when working with this type of concrete, and I will briefly try to explain some of these:
CRC – abbreviation for Compact Reinforced Composite – this is the special type of UHPC we use at Hi-Con. It was developed (and patented) at Aalborg Portland by Hans Henrik Bache in 1986 and was the first UHPC of its kind, combining a compressive strength of more than 150 MPa with high tensile strength and ductility – which is only possible due to a high content of steel fibers – and closely spaced reinforcement bars to achieve the same behavior as steel, but with the advantages of concrete. At that time, terms like UHPC were not really used; instead, the term High Strength Concrete (HSC) was used. Initially, there was a strong focus on developing compressive strength, but it quickly became apparent that other properties such as durability or ductility were just as important, and the term High Performance Concrete (HPC) was coined.
The idea behind this development was that the concrete was designed for a specific application, which did not necessarily require high compressive strength. Therefore, the focus was directed towards properties like high tensile capacity, long durability, extreme formability, or similar.
In the mid-90s, a number of other commercially available high-strength concretes were developed, such as Ductal (Lafarge), BCV (Vicat), and BSI/Caracem (Eiffage and Sika), and in an attempt to classify these different types of concrete, the term Ultra High Performance Concrete (UHPC) was introduced to characterize concretes with a compressive strength of more than 140-150 MPa.
UHPC is generally characterized by high compressive strength, low permeability, high formability, and a flexural strength of more than 25 MPa. This is achieved by having a high binder content (900-1500 kg per m3), a high content of micro silica and glass powder, and a matrix where the largest sand grains are often less than 0.25 mm. As the water-to-powder ratio is typically below 0.2, an extremely effective plasticizer is required, and to ensure the necessary formability of the elements, fibers (often steel fibers) are used in amounts between 100 and 300 kg per m3. Traditional mixers and mixing equipment can be used, but due to the very low water content, long mixing times are necessary to achieve a homogeneous mass. As many UHPFRC concretes are used as a combination of fibers and pre-stressed concrete, curing often takes place at high temperatures, improving mechanical properties and ensuring that most shrinkage occurs before pre-stressing.
CRC – the type of concrete we use at Hi-Con – is not a typical UHPC. In our test trials with cubes using local aggregates, the average compressive strength measures around 150 MPa, but since the Eurocode is based on measurements of compressive strengths on 150x300 mm cylinders, we use a characteristic strength of just 110 MPa in our designs. The matrix has a high binder content, a high content of microsilica, and a water-to-binder ratio between 0.15 and 0.18. Additionally, we use sand grains up to 4 mm, which means that the binder content in CRC can be reduced compared to UHPFRC, which uses only very fine sand. This gives us slightly lower strength but a more economical mix with less shrinkage.
The CRC mix is self-compacting, but with its high fiber content (typically from 120 to 230 kg/m3) and its high viscosity ensuring good fiber distribution, CRC is best suited for prefabricated elements where vibrations can be applied to improve compaction.
30 years of experience in UHPC sounds good, but if you are not careful, it can turn out to be 5 years of experience that has been reused over the past 25 years. You constantly need to acquire new knowledge. We proudly state that we are up-to-date with the latest developments in UHPC, but paradoxically, we use almost the same CRC formula that was developed in 1986.
Over the years, we have made some improvements to the material – in terms of improved workability, cost reductions, and reduced need for finish work – but if we made drastic changes to the composition of CRC, we would have difficulty using the extensive documentation we have developed over the years. Although our mix does not look much different than it did 20 years ago, we have gotten to know our concrete very well – both in terms of its strengths and limitations – and this allows us to design and produce very complicated elements while providing the necessary documentation.
For some of our products, we produce mixes that are slightly different from the original CRC formula, but currently, we use the base mix for 95% of the elements we produce. This enables us to identify where we can add value in a construction project – or whether our product is not suitable for a given project. And we can confidently say that there are still plenty of projects that are well-suited for CRC!
Lastly, to answer the question in the title: Yes, we consider ourselves to be among the world leaders in UHPC. This comes from being a commercial company that has designed and produced CRC every single day for almost 20 years – often in competition with steel and traditional concrete – and if we were not good enough at it, we would not exist today.
Don't hold back
CONTACT US IF YOU WANT TO KNOW MORE ABOUT UHPC