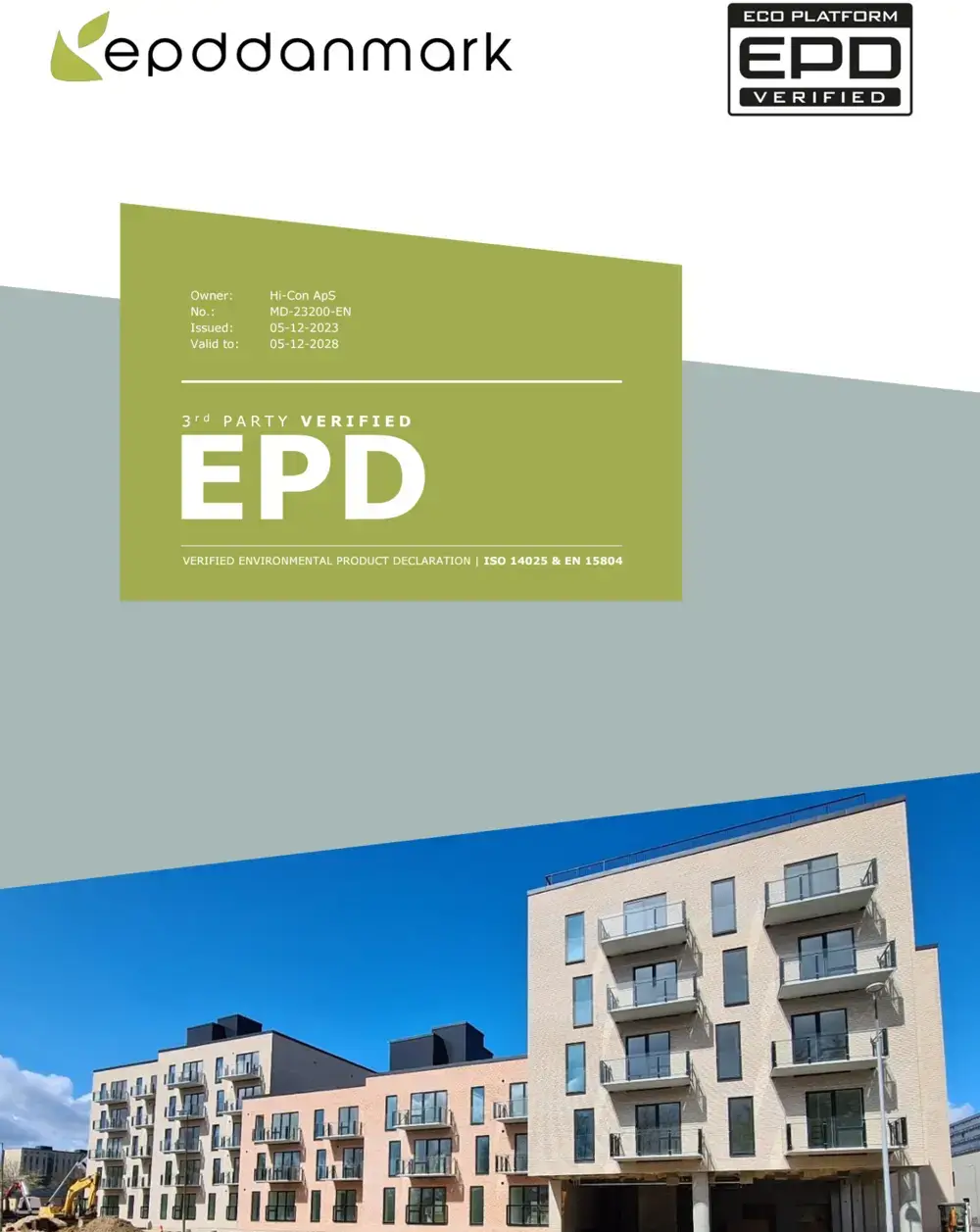
20. December 2023
In one of our previous posts: Do we really a need another guideline for Ultra High Performance Concrete?, we mentioned that Hi-Con has applied for an ETA, and now we are ready to add a CE marking to our balcony elements. It took a bit longer than expected, but in the following post, we will explain a little more about what this means, why we decided to do this, and how the process has been.
Before you dive into the post, we want to point out that this blog post does not contain much information specifically about Ultra High Performance Concrete—it is instead a description of how we have decided to proceed with the documentation of our products and what was necessary.
You can read more about Ultra High Performance Concrete here:
One of our first CRC balcony projects from 1998
In some countries, however, it is very clear that CE marking would likely be very beneficial for the sale of our products. When we provide our own documentation for a project, the engineer must assess and determine whether this level of documentation is sufficient—in cases where the product has a CE marking, it is unnecessary for the engineer, owner, or building authorities to evaluate whether our balconies are suitable for installation, as this has already been done by another party. This way of thinking has been particularly evident in Finland and England. In London, we had a project where our solution was approved by the parties we had in mind: the owner, the engineer, the architect, and the building authorities, BUT the insurance company then decided that they would not insure the building if the balconies were not CE marked! We have quite often explained our design methods and material properties—but rarely to an insurance agent. In this case, the interest in understanding our explanation and making a decision in favor of our product was not really there. Unfortunately.
Currently, we are looking at a few projects in Germany, and it is another market where we hope the CE marking will be useful—although we expect there may be a need for additional tests in the form of a special approval.
Previously, we have often been asked why we do not obtain national approvals—for example, from the British Board of Agreement—but we have been reluctant to do this, as any approval would typically be limited to a specific product and specific dimensions. The CE marking is different because it covers a larger market and has a broader scope. With the hope that such a certification would facilitate "acceptance" in our new markets, we decided to start the process. We began the process in the spring of 2014—and did not expect it to take nearly five years.
Since it was us compiling the EAD—in collaboration with ETA Denmark—we had many options regarding what to include, and apparently, we chose the complicated route.
The EAD outlines the documentation methods and acceptance criteria for a construction product and must cover the essential characteristics. What constitutes "essential characteristics" is open to interpretation, and we could perhaps have settled on a few parameters like compressive strength, tensile strength, and water permeability. However, our concern was that even if you have a UHPC product that meets these requirements, you could still have a poor product. We wanted to provide a description where the producer gets a product suitable for use if all these requirements are met. So, in our case, the EAD includes an extensive list of essential characteristics that we consider important for performance (examples are compressive strength, form of stress-strain curve in compression after maximum load is achieved, stiffness, ductility, tensile strength, creep and shrinkage, freeze/thaw resistance, carbonation, fiber distribution, chloride penetration, and fire resistance). Additionally, design calculations must be verified through full-scale tests.
After the EAD was accepted by the European Commission (in May 2016), the next step was to prepare an ETA, which was then assessed based on the EAD. While we already had many of the test results, additional tests were still necessary to document the balconies. For instance, we have conducted extensive tests on high-temperature behavior over the years, but these tests were typically carried out at universities. Since we needed a classification report, we had to conduct a new test at a laboratory accredited for fire testing of load-bearing structures. The additional tests and compilation of all documentation took another year, but in May 2017, our ETA was accepted. The ETA is only 13 pages, but hundreds of pages were submitted to ETA Denmark as documentation annexes. After this, we "only" needed certification from Dancert to CE mark our balconies.
Compared to other concrete producers, our DoP is somewhat complex, and many more parameters are listed. We have been asked why we don't limit it to just a few parameters to make it easier for ourselves (which certainly would have reduced the time it took from the start of the EAD to the final certification), but we actually did this on purpose. We believe ultra-high-performance concrete (UHPC) is complex, and many very different properties combine to create a good product. We have already seen examples where other producers—not familiar with UHPC—have copied some of our slender designs. They have copied our dimensions and produced elements based on a 100 MPa concrete. This is not difficult to do, but if you do not provide the correct ductility by including steel fibers—or if you do not consider the risk of explosive spalling during fire exposure, there is definitely a risk involved in structural applications. We do not mind competition (there is not much we can do about it), but we want them to do it the right way by realizing that compressive strength is not the only property you need to consider for a reliable design in UHPC for projects like the one below.
Our CE marking is very new, so we look forward to seeing how it is received in the market—or if it has any effect at all. If the CE marking facilitates the approval of our balconies, we will certainly consider doing something similar for other products such as stairs and facades. Hopefully, it will be a shorter process next time, as our EAD, ETA, and CE marking mostly deal with the approval of the material—very little is actually product-related.
Interested in learning more about Ultra High Performance Concrete?
FILL OUT THE FORM AND WE'LL GIVE YOU A CALL